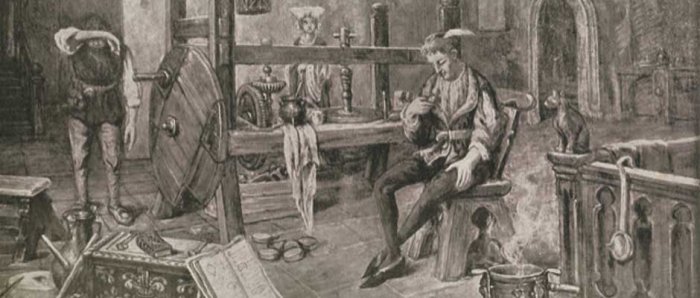
Evolution et révolution du secteur diamantaire | FR
Les diamants sont connus depuis des millénaires, mais selon les sources historiques, la taille commence seulement il y a plus ou moins 550 ans, au XVème siècle. Les balbutiements de la technologie pour travailler une matière si dure ont été décrits par Pline l'Ancien de façon quelque peu exotique. Mais ce sont surtout les mystères et les légendes entourant cette pierre exceptionnelle, à l'origine divine pour les anciens grecs qui l'interprétaient comme poussière d'étoiles tombées du firmament ou encore larmes des dieux, qui retardent les progrès de la taille.
La deuxième évolution fut le « dop à lumière ». Un faible courant électrique relie le plateau de polissage en fer à la pince ou dop aussi en fer. Le diamant n'étant pas conducteur, tant qu'il constitue la matière intermédiaire reliant le plateau au dop, aucun signal électrique n'est produit. Lorsque la facette est terminée, le bord de la griffe en métal retenant le diamant touche le plateau de polissage, créant ainsi la connexion permettant à la lumière d'apparaître. La propagation de ce signal électrique fut à la base de l'automatisation. Au signal, un levier soulève le dop qui tourne le diamant présentant alors une autre facette à tailler et ainsi de suite. La vraie première machine de taille semi-automatique fut créée par la Bell Téléphone en 1967, sans doute née trop tôt car l'époque des « Golden sixties » n'imposait pas l'automatisation puisqu' aucune concurrence réelle menaçait. Mais dans les années 80 la situation change avec beaucoup d'innovations technologiques non seulement en Belgique mais aussi aux Etats-Unis, en Angleterre avec Piermatic et en Israël. La DTC propose le rotang, sorte d'œuf de Colomb : la tête tourne lentement, le diamant se trouvant à un moment donné dans la bonne position. Néanmoins, il n'a pas eu le succès escompté. Le dernier-né et la plus efficace des machines de taille semi-automatique est sorti des ateliers du WTOCD, c'est l'Octopus du début des années 2000. L'expertise du brut s'est aussi améliorée de façon spectaculaire, la jauge classique et le proportionscope disparaissent et sont remplacés par des outils d'analyse électronique tels que le Sarin, Oggi, Reflex et Hélium qui calculent et proposent toute possibilité de taille, évaluent la perte, le rendement, le tout pouvant être connecté et accompagné de la fameuse liste hebdomadaire de Rapaport. Les nouvelles normes, toujours plus strictes, obligent à la création de nouveaux outils de polissage d'une extrême précision. Le forage au laser débuté dans les années 70 est maintenant utilisé pour le clivage, le sciage et la préforme avec une performance de plus en plus poussée causant moins d'accidents et de perte et tournant 24/24h. Le débrutage a été également automatisé depuis le système de double tête. Plusieurs sociétés sont présentes sur cette partie du marché mais c'est les ateliers du WTOCD qui produisent le plus performant, l’EOS. La véritable révolution vient du centre de recherche, scientifique et technologique du diamant WTOCD crée en 1977 où une équipe d'ingénieurs, physiciens et techniciens effectue des recherches fondamentales sur le diamant brut, son débrutage et sa taille automatique notamment. Compte tenu des exigences de précision inscrites dans les nouvelles normes, le WTOCD a dû mettre au point des nouveaux appareils de réglage de haute précision à destination du tailleur. Du Morgana pour la mise au point, au micromètre près, à la pince de taille et à l'Avalon, pour visualiser la finesse du travail de polissage sur un écran. Ces accessoires sont devenus indispensables dans l'atelier. Les tailleurs méritent notre plus profond respect car ils peuvent obtenir des résultats stupéfiants avec des moyens malgré tout très limités sur cette matière extrême qu'est le diamant. Au fil des années, le WTOCD a développé des outils pour aider le tailleur, mais la taille reste une tâche ardue, qui exige des années de formation et d'expérience pour maîtriser le métier. La détection des synthèses dans les mêlées et la manipulation de petits brillants sont des problèmes cruciaux que le centre a résolu grâce aux différents instruments mis à la disposition du bijoutier et du diamantaire tels que le D-Screen, M-Screen, J-Screen, D-Tect et Alpha Diamond Analyzer. Quant à l'évaluation - proportions, couleurs et finitions - elle est établie aussi à partir d'instruments de haute précision créés par le WTOCD. Lors de la taille, classiquement, la première étape est confiée à des instruments hautement sophistiqués qui déterminent la solution de taille la plus optimale. Puis c'est le tailleur qui passe à la taille proprement dite avec le risque induit d'imprécisions car cette action est peu automatisée. La dureté du diamant entraîne la nécessité de la recherche du grain, de la direction la moins dure. De plus, le diamant chauffe considérablement lors de la taille. Et cette élévation de la température est le facteur qui limite une automatisation complète du processus de taille. Car le diamant est un très bon conducteur de chaleur et transfère sa température au support métallique. Ce support se gonfle, rendant impossible une mesure précise. N'oublions pas que nous travaillons avec une précision du centième de millimètre. Ce travail intensif est la raison du déplacement de l'industrie vers des pays à bas salaires. Le moulin de taille du XXIème siècle, baptisé Phénix, possède deux disques, l'un en acier pour la taille et un autre en céramique pour la finition. Ce nouveau système automatique ne requiert aucune formation pour le tailleur. Il se charge de la planification et taille automatiquement la forme choisie. Le processus est indépendant du grain et extrêmement rapide et ne passe pas par une recherche préalable de la structure cristalline. Il fonctionne en deux étapes : une phase d'ébauche où le diamant est taillé jusqu'à 100 microns du modèle planifié et une phase où les facettes sont rendues transparentes (généralement jusqu'à 20 microns de la profondeur finale). La température lors de la taille reste limitée à 30-35 °C comparée aux 100° à 250° de la taille classique ; la rapidité de la taille en est alors plus que triplée. Quelques exemples pour illustrer la vitesse de Phénix : une marquise de 0,88 et issue d'un diamant brut de 2,67 et un brillant de 0,54 et provenant d'un brut de 1,99 et. Pour la marquise, les 53 facettes ont nécessité 63 minutes grâce au Phénix tandis que les celles du brillant a pris 56 minutes pour l'ébauche et 57 minutes pour la taille finale. La taille classique de ces deux pierres nécessiterait plus d'une journée (surtout la marquise) pour obtenir un résultat similaire. Autre comparaison impressionnante : Phénix peut tailler une pierre de 100 carats dans le même laps de temps que celui nécessaire pour tailler une pierre de 5 carats. En conclusion, le WTOCD a développé une technique de taille révolutionnaire permettant la taille automatique, indépendant du grain, à froid et ultra-rapide, avec une précision incroyable allant jusqu'à 0,05 ° pour toutes les formes y compris la taille cabochon. La pierre après avoir été sertie sur un support à l'aide d'un liant UV et ajustée à l'aide de l'ordinateur, la pierre glisse littéralement sur des vagues de liquides lubrifiants contenant des millions de microbilles de diamant synthétique. La pierre reste à quelques microns du disque où se crée un véritable film abrasif. Le disque ne tourne qu'à 1.000 tr/mn, ce qui est environ un tiers de la vitesse normale d'un disque de taille. La pression sur le disque n'est que de 5 à 10 Newton comparée à plus de 40 à 50 Newton et souvent bien plus lors de la taille classique. La pierre n'est alors chauffée qu'à 35°C maximum. Le résultat est une taille aux proportions et à la symétrie classées « excellent » selon les dernières normes, le tout à une vitesse moyenne dix-huit fois plus rapide que celle de la taille classique. Quant au polissage, il doit être provisoirement exécuté de manière classique pour répondre aux exigences de qualité actuelle, comparées aux normes d'il y a à peine quelques décennies. Suite à une baisse importante de l'activité du département des certificats HDR et du repli du chiffre d'affaires de l'AWDC depuis plusieurs années, l'AWDC a dû vendre le centre WTOCD à la société HSTechnology.
|